Packaging Machine Repair Service for All Brands and Designs of Equipment
Comprehending the Secret Components and Repair Strategies for Product Packaging Maker Maintenance
Efficient maintenance of product packaging makers rests on a detailed understanding of their crucial elements, including the structure, drive system, and sealing devices. Acknowledging typical maintenance problems, coupled with the execution of preventative techniques and troubleshooting strategies, can substantially enhance maker reliability. Furthermore, the selection of repair work techniques, including the usage of OEM parts and the importance of certified professionals, plays an important duty in decreasing downtime. To genuinely grasp the complexities of these systems and their upkeep, one have to consider the wider effects of overlooking these necessary practices.
Trick Components of Packaging Devices
Packaging devices contain several essential elements that collaborate to guarantee reliable and effective packaging processes. At the core of these devices is the framework, which supplies structural integrity and houses the various operating components. The drive system, usually a mix of electric motors and gears, assists in the motion of components, making it possible for exact operation throughout the packaging cycle.
An additional crucial element is the conveyor system, which carries items through different phases of the packaging process. This is typically matched by sensing units and controls that check the setting and speed of products, ensuring synchronization and decreasing mistakes. The filling up system is crucial for properly dispensing the right quantity of product right into packages, whether in fluid, powder, or strong type.
Sealing devices, including warm sealers or sticky applicators, play a vital function in securing bundles, preventing contamination and prolonging life span. In addition, labeling systems are important for providing needed item information, ensuring conformity with laws. Ultimately, the control board, furnished with user-friendly user interfaces, enables operators to handle device functions, monitor performance, and make changes as needed, ensuring optimum productivity and effectiveness in packaging procedures.
Common Maintenance Issues
Effective procedure of packaging makers relies greatly on regular upkeep to avoid usual concerns that can interrupt manufacturing. Amongst these concerns, mechanical damage is prevalent, specifically in elements like seals, conveyors, and electric motors, which can lead to unanticipated downtimes. In addition, misalignment of components can cause inefficient procedure, creating items to be incorrectly packaged or damaged during the process.
One more usual maintenance concern involves the build-up of dust and debris, which can hinder the device's sensors and moving parts. packaging machine repair service. This not only affects efficiency yet can additionally posture safety and security threats. Lubrication failings can lead to enhanced friction, resulting in overheating and eventual part failing.
Electrical problems, typically coming from loose connections or damaged circuitry, can disrupt machinery functions, resulting in significant production hold-ups. Last but not least, software program glitches due to inappropriate arrangements or outdated programs can prevent the device's procedure, necessitating immediate intervention. Addressing these usual maintenance concerns proactively is necessary for making sure optimal efficiency and longevity of packaging equipment.
Preventative Maintenance Approaches
Carrying out preventative maintenance methods is important for sustaining the effectiveness and reliability of packaging equipments. These methods encompass a methodical approach to maintenance, concentrating on the regular examination and servicing of equipment to preempt possible failures. he said By adhering to a set up upkeep program, operators can determine wear and tear on parts before they cause substantial failures.
Crucial element of a preventative maintenance method consist of routine examinations, lubrication, part, and cleaning replacements based upon supplier referrals. Using lists can streamline this process, guaranteeing that no necessary tasks are forgotten. In addition, maintaining precise documents of upkeep tasks help in tracking the equipment's efficiency over time, helping with notified decision-making relating to future upkeep requirements.
Educating personnel on the value of preventative maintenance improves conformity and promotes a culture of positive treatment. Carrying out a predictive maintenance component, utilizing data analytics and sensing unit modern technology, can better maximize equipment efficiency by anticipating failures before they take place.
Repairing Methods
When confronted with breakdowns or ineffectiveness in packaging machines, using methodical troubleshooting techniques is essential for recognizing and fixing issues promptly. The primary step in reliable troubleshooting is to establish a clear understanding of the machine's functional parameters and efficiency metrics. This includes reviewing the maker's specifications, along with any mistake codes or notifies shown.
Next, operators need to carry out an aesthetic assessment, looking for evident indicators of damage, wear, or imbalance. This usually includes taking a look at belts, sensing units, and equipments to identify possible causes of malfunction. Collecting functional data, such as production prices and downtime logs, can also offer understandings right into recurring problems.
When possible troubles are identified, utilizing a sensible technique to separate the root reason is crucial. This may need screening specific parts or systems in a controlled manner. Engaging in discussions with operators that engage with the machinery frequently can generate valuable responses regarding uncommon behaviors or patterns.
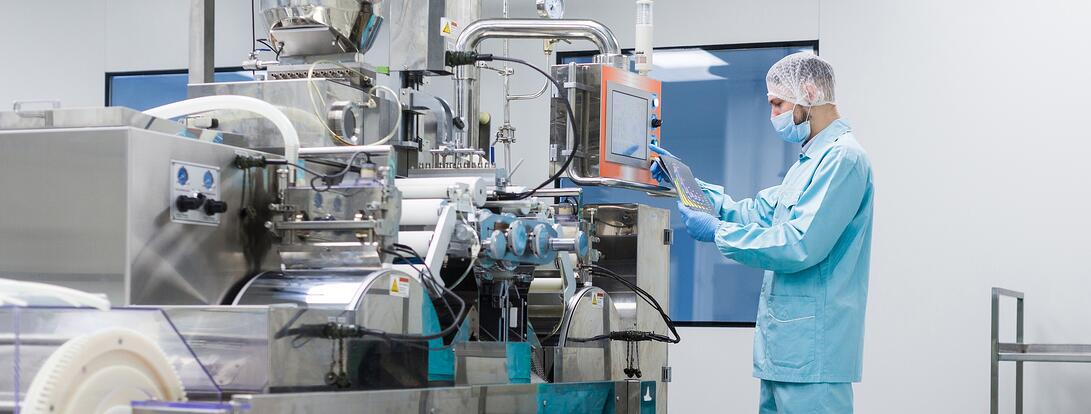
Repair Work and Substitute Ideal Practices
A detailed understanding of repair work and replacement best practices is essential for maintaining the durability and efficiency of product packaging view website devices. Frequently evaluating the problem of maker components permits prompt intervention, preventing even more considerable concerns that can result in costly downtimes.
When fixings are required, it is important to use OEM (Original Equipment Maker) parts to you can check here make sure compatibility and efficiency. This not only maintains the stability of the equipment but additionally upholds guarantee arrangements. Furthermore, it is suggested to maintain a stock of critical spare components to facilitate quick substitutes and minimize operational interruptions.
For complex repair work, involving certified service technicians with specialized training in product packaging machinery is suggested. They have the expertise to identify problems properly and execute repair work effectively. In addition, documenting all repair work activities and components substitutes is crucial for maintaining an extensive upkeep background, which can assist in future troubleshooting.
Last but not least, applying an aggressive method, consisting of routine evaluations and predictive maintenance methods, improves the reliability of packaging machines. By adhering to these ideal practices, organizations can guarantee ideal device performance, reduce operational risks, and prolong tools life-span.
Conclusion
To conclude, a complete understanding of product packaging machine parts and efficient maintenance methods is crucial for optimum efficiency. Routine assessments and using OEM parts can dramatically decrease downtime, while a well-documented maintenance history cultivates aggressive treatment. Utilizing licensed professionals further enhances repair quality and reliability. By implementing these practices, companies can make certain the durability and effectiveness of packaging devices, ultimately adding to boosted functional productivity and reduced prices.
Efficient maintenance of product packaging equipments pivots on an extensive understanding of their crucial elements, including the framework, drive system, and securing mechanisms.Effective operation of product packaging equipments counts greatly on normal upkeep to protect against usual concerns that can interfere with manufacturing.Carrying out preventative maintenance techniques is essential for maintaining the effectiveness and dependability of packaging machines. In addition, keeping precise records of maintenance activities help in tracking the equipment's efficiency over time, helping with informed decision-making regarding future upkeep requirements.
